How cable ties are made? This is a question many of us might not have considered before. When bundling wires, cables, or other miscellaneous objects, one tool often comes to mind – cable ties.
As a product of high-performance plastics, nylon cable ties are recognized for their excellent mechanical properties, heat resistance, corrosion resistance, and UV resistance. As a result, they are widely used in electronics, power, transportation, automotive, and other fields.
Despite their seemingly simple appearance and one-piece design, the manufacturing process of these cable ties is both complex and intricate. In this article, we will break down how cable ties are made, to give you a closer look into the process behind their production.
What Is Cable Tie
Cable ties, also known as zip ties, are thin strips made from polyamide 66 or nylon 66. These cable ties have a unique design: a hole-shaped head equipped on one end, and the other end is a gradually narrowing tail. The belt body of the tie is lined with neat teeth, and inside the tie’s head is a pawl. When you thread the tail into the head’s hole and pull tight, the pawl catches onto the teeth, forming a secure loop that’s ready for use.
How Cable Ties Are Made
Step 1: Cable Ties Mold Manufacture
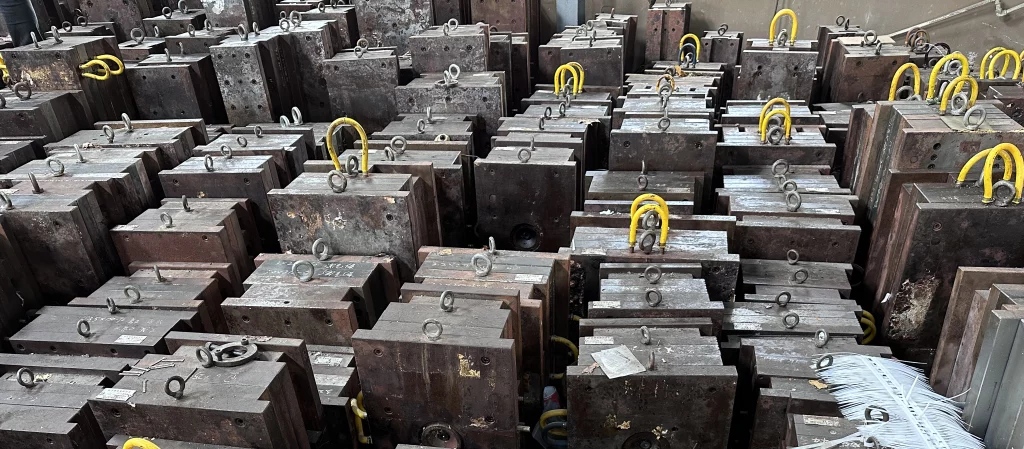
The process begins with the creation of precise molds. One cable tie size needs one mold. Each of these molds contains some individual cavities, with each one set to shape a single cable tie. Depending on the design and size of the cable ties, the process could require a unique cavity, or in some cases, several cavities. It’s interesting to note that the number of cavities in a mold can be different, for instance, a mold for 5-inch length cable ties may hold up to 150 cavities, while one for larger 70-inch length cable ties might house just 4 cavities.
To ensure a traceable operation, the cable tie manufacturer often identifies each mold with a unique mark, perhaps a number, a letter, or even a logo. These identification markers play a vital role during the quality control process. They assist in pinpointing defective or blocked molding cavities, which might affect the quality of the cable ties.
At NIKE Plastic, we have a dedicated commitment to efficiency and quality. For each size of cable tie, we prepare two identical sets of molds. This way, should any mold faults be identified during quality checks, we can promptly switch to our backup molds, ensuring no delay to our clients.
The specific design, shape, and color of a cable tie are largely determined by the specifics of the molding cavity utilized in its production. Each cable tie manufacturer brings their unique approach and techniques to the process, resulting in distinctive shapes, colors, and lengths of cable ties. At NIKE Plastic, we pride ourselves on the exceptional diversity and quality of our cable tie production.
Step 2: Raw Material Processing
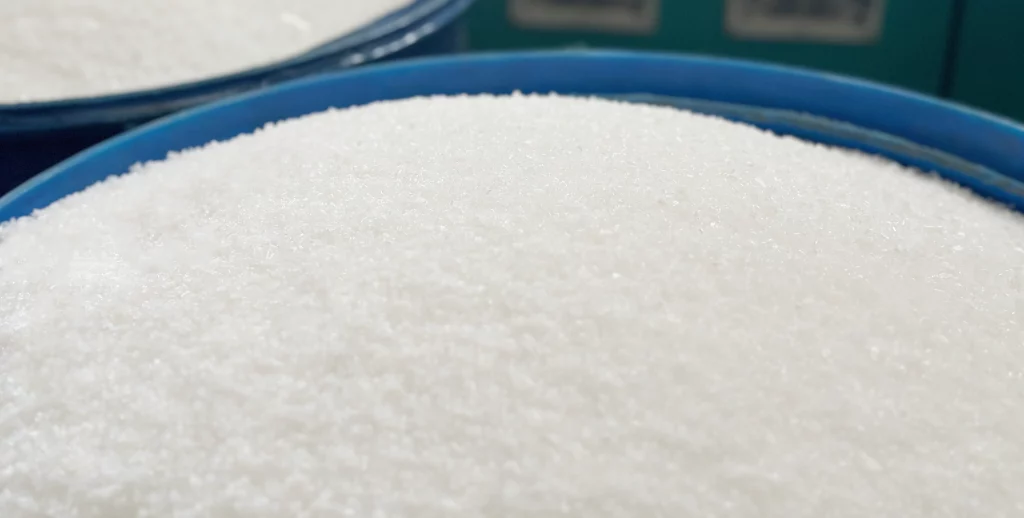
The creation of standard nylon cable ties begins with polymer Polyamide 66 (nylon PA66) particles. The first part of this stage involves placing these particles into a dryer’s hopper. Using advanced drying technology, excess moisture within the nylon is removed. Why is this crucial? Moisture can lead to instability within the polyamide molecules, negatively affecting both their physical and mechanical properties. Hence, this drying process is an essential step in ensuring the quality of our cable ties.
Step 3: Injection Molding
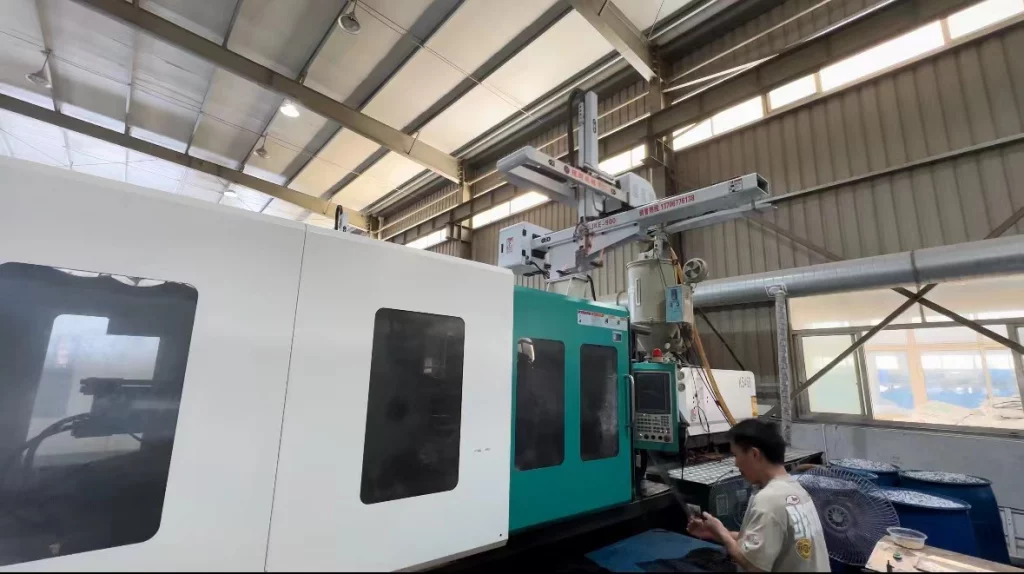
3.1
The injection molding, also the magic begins during the injection molding stage. The pre-treated nylon particles(PA66) are transferred into individual injection machines through a complex system of elevated pipelines, ensuring speedy and accurate transportation from the hopper to each injection machine across the factory.
3.2
Inside the injection machine’s screw barrel, as the screw rotates and the outer wall of the barrel heats, nylon is heated to over 260℃, transforming the particles into a molten state.
3.3
Then the mold close, and the injection seat move forward, the nozzle adheres to the mold’s sprue, and finally, the screw propels forward, injecting the molten nylon into a closed lower-temperature mold at high pressure and speed. The molten nylon is pushed into each cavity to create the shape of the cable ties.
3.4
After a period of pressure holding and cooling, the plastic solidifies. The mold then opens, and the product is removed.
PS: The time for pressure holding is to prevent backflow of melt in the mold cavity, supplement material in the mold cavity, and ensure the product has a certain density and dimensional tolerance.
The process of injection molding bears similarities to using a syringe for injection. The mechanism relies on the thrust of a screw (or plunger) to inject the molten plastic, which has been plasticized into a closed mold cavity. Upon cooling, the product takes shape.
Injection molding is a cyclic process, with each cycle involving quantitative feeding, melt plasticizing, pressure injection, mold filling, cooling, and mold opening for part removal. Once the zip tie has been removed, the mold closes again, commencing the next cycle.
It’s essential to remember that the primary requirements for injection molding are plasticizing, injection, and molding. Plasticizing ensures and maintains the quality of the molded product. To meet the requirements of molding, injection must ensure sufficient pressure and speed. Given the high pressure of injection, correspondingly high pressure is generated in the mold cavity, necessitating a sufficiently large clamping force. Thus, it’s evident that the injection device and the clamping device are critical components of the injection machine.
Step 4: Robotic Removal of Cable Ties
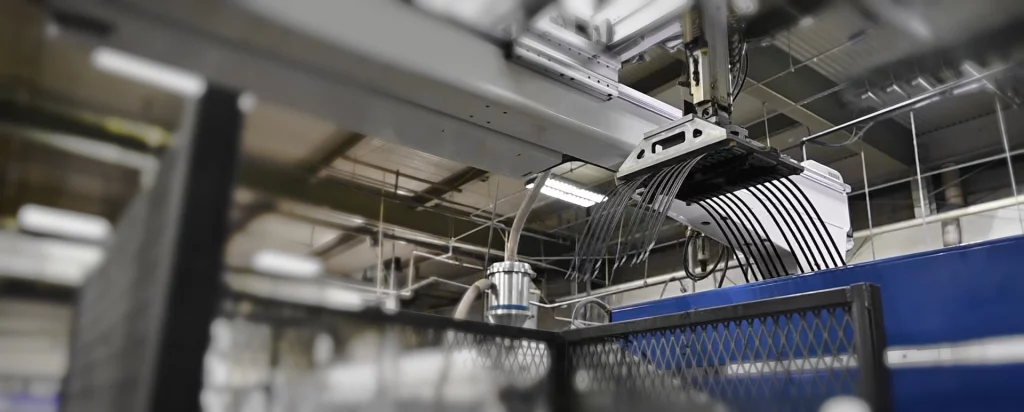
Once the injection molding is complete, the newly formed cable ties are promptly picked up by precision robots and placed onto a conveyor belt, ready for immediate packaging. It’s an operation demanding both speed and care – the operators at each machine station need to self-inspect each zip tie. To ensure that each cable tie is complete, correctly formed, and up to par in terms of quality and appearance.
Step 5: Moisture Adjustment of Cable Ties
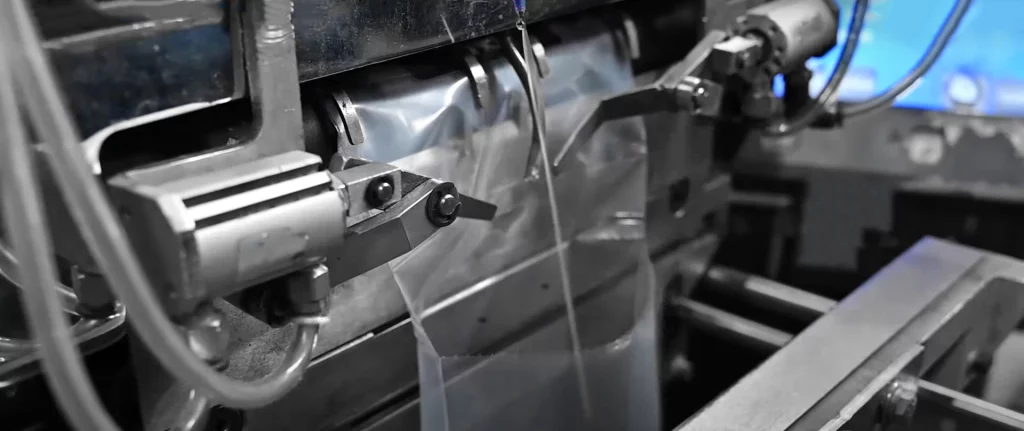
Cable ties emerging from the injection machine are completely dry. While this state makes them firm, it also leaves them brittle, and lack of toughness. To strike a balance between strength and toughness, we need to reintroduce some moisture during the packaging process, about 2% of the total tie weight. This small but essential adjustment ensures the nylon cable ties retain their necessary toughness without sacrificing their inherent strength.
Step 6: Quality Control and Quality Inspection of Cable Ties
Quality control procedures are a fundamental aspect of the cable tie production process. At NIKE Plastic, we adhere strictly to the ISO9001 quality management system to ensure the quality and performance of our cable ties. Each stage of tie production is meticulously monitored, and our production complies with the zip tie industry standard QB/T4494-2013 and GB/T2828.1-2012 sampling standard for rigorous sampling inspection.
Our quality control measures begin even before the manufacturing of the ties. We perform thorough inspections on the raw material, PA66, to ascertain it meets all requirements. During the injection molding and mold manufacturing stages, we carry out machine calibration and testing to ensure the accuracy of the produced zip ties’ size and shape. In the automatic extraction and packaging phase, we ensure the correct specification model for each tie. Lastly, in the final factory acceptance test stage, we conduct comprehensive tests for strength, durability, high and low-temperature resistance, and buckle force, further guaranteeing the performance and reliability of our cable ties.
Conclusion
In the full process of creating nylon cable ties, each step is critically important. From material selection and mold manufacturing to equipment optimization, process adjustments, and quality inspections, every phase plays a key role in producing high-quality, reliable nylon cable ties.
As a professional cable tie manufacturer with advanced production equipment and extensive experience, NIKE Plastic Co., Ltd. is committed to continually refining our production process and enhancing the quality and performance of our products. We believe that as the cable tie market continues to expand, advancements in the production of nylon cable ties will also keep progressing. Staying attuned to market demands and emerging technologies, we aim to innovate and optimize our practices, delivering our customers the highest quality and most reliable cable ties!