The creep of cable ties is a phenomenon where the cable ties undergo a permanent deformation over time under sustained mechanical stress. Understanding this property is crucial for the use of polymer materials like nylon. Nylon cable ties are widely used in various bundling and securing applications, and their long-term reliability and durability, deciding how long do cable ties last, are directly affected by creep. In engineering applications, cable ties need to maintain structural integrity over extended periods, meaning they should neither loosen nor break. Comprehending the creep behavior of the tie material can significantly aid in better selection and utilization of cable ties.
What is Creep?
Creep refers to the tendency of a solid material to slowly and permanently deform under the influence of constant stress over time. It occurs at a rate that is typically very slow, but it can become significant, especially under high stress or elevated temperatures. This process is often observed in materials such as polymers (the material of cable ties) when subjected to long-term load or constant environmental stress.
In simple terms, if you apply a constant force to a material like a nylon cable tie, it will initially deform or stretch a little. Over time, even if the force doesn’t increase, the material will continue to stretch or deform more. This gradual, time-dependent deformation is what we call creep. It’s a crucial factor to consider in many engineering and design applications, as it can affect the long-term performance and reliability of materials and products.
Creep is also one of the mechanical performance indicators for cable ties. In practical applications, such as securing and bundling cables with cable ties, creep can lead to a decline in performance, thereby affecting their functional efficacy. For nylon materials, understanding creep is particularly critical. The molecular structure of nylon facilitates alignment and slippage under stress, leading to creep under prolonged loading. Different types of nylon, such as nylon 6 and nylon 66, have distinct molecular structures and arrangements, resulting in varied creep behaviors. Of course, many factors influence the creep of nylon.
3 Key Factors Affecting Creep of Cable Ties
Stress
The stress significantly influences the creep behavior of cable ties. This can be better understood from the following chart.
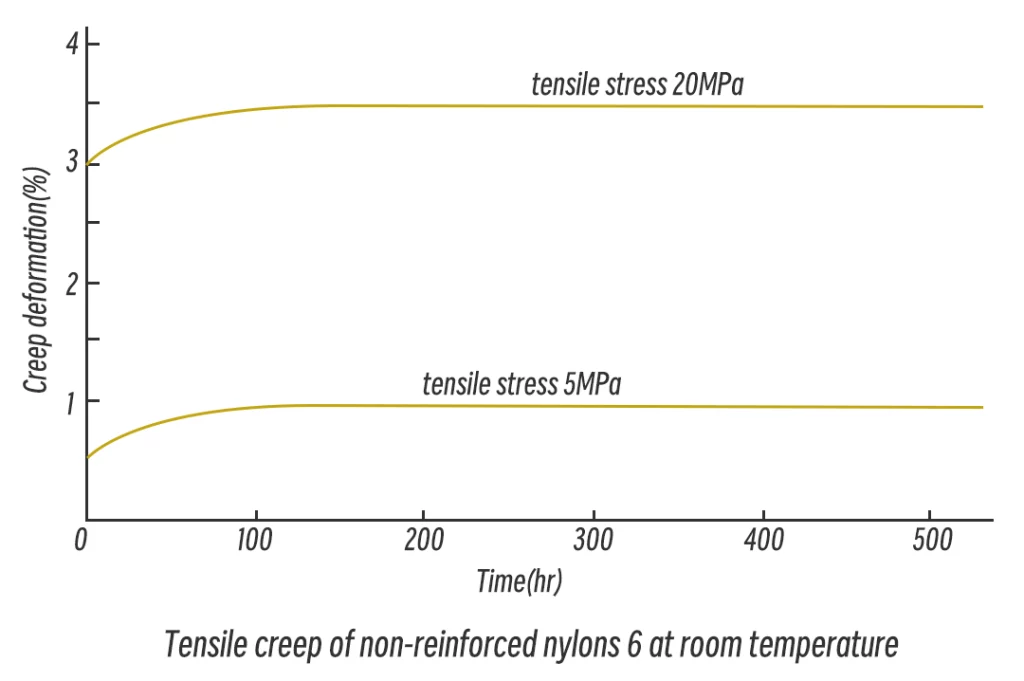
The chart illustrates the change in creep deformation over time for nylon 6 and nylon 66 under different tensile stresses (5 MPa, and 20 MPa).
From the chart, it is evident that at higher stress(20 MPa), the creep deformation of nylon 6 is notably greater than at lower stress(5 MPa). This indicates that when nylon is subjected to higher stress, the rate of change in its internal structure is faster, leading to greater deformation. Moreover, the rate at which this deformation accumulates over time is also quicker. This means that under the same duration, nylon 6 cable ties experiencing higher stress may be closer to their failure point.
Temperature
The following chart displays the impact of different temperatures on material creep deformation under the same tensile stress (20 MPa). It is evident that temperature significantly affects the creep behavior of nylon materials.
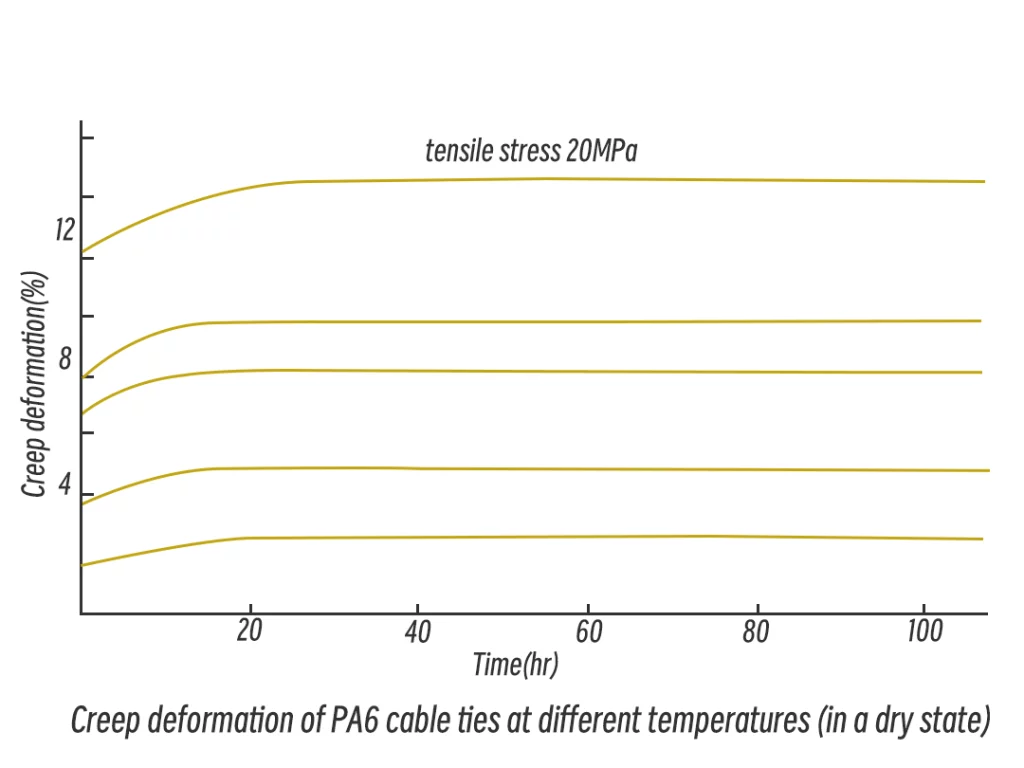
As the temperature increases, the material’s creep deformation correspondingly rises. At 40°C, the material exhibits relatively low creep deformation, while at 150°C, the deformation is considerably more pronounced. This suggests that higher temperatures make the nylon’s polymer chains more prone to movement, leading to easier deformation under the same loading stress.
At elevated temperatures, the increased thermal motion within the material weakens the intermolecular interactions, thus allowing for easier displacement under external forces. Therefore, when designing cable ties or components for use in high-temperature environments, considering the material’s creep is crucial. For instance, we might select heat-resistant cable ties to ensure the structure’s reliability and stability over long-term use.
Material
The chart below presents a comparison of the creep behavior between two different nylon cable tie materials, Nylon 6 (PA6) and Nylon 66 (PA66), at various temperatures. It can be observed that, at the same temperature, Nylon 66 typically exhibits lower creep deformation than Nylon 6, especially at elevated temperatures where the difference becomes more pronounced.
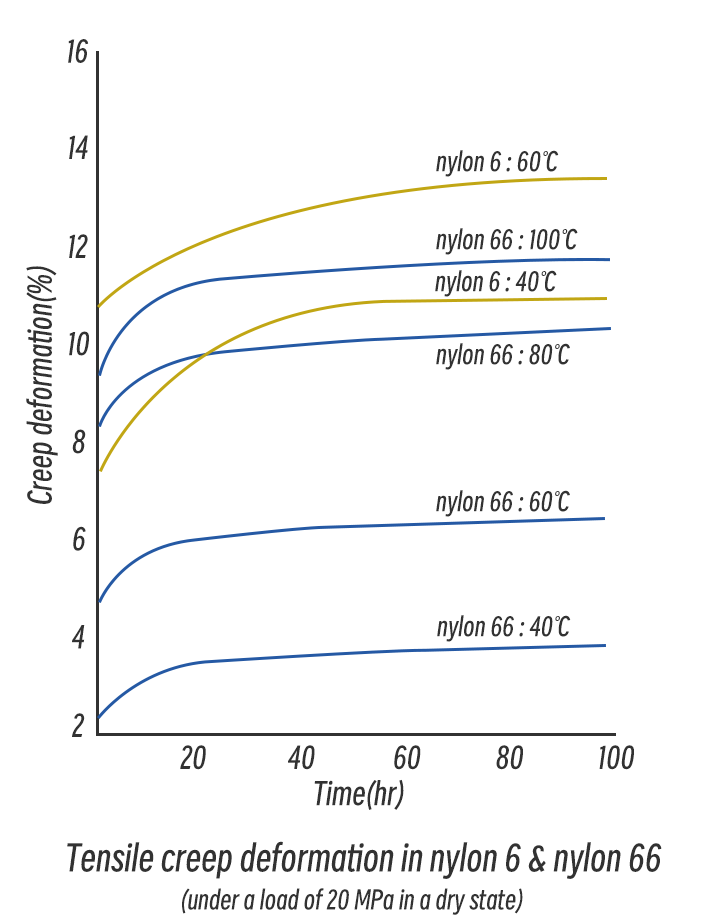
The type of nylon directly affects its creep behavior:
Nylon 6 (PA6): This material typically demonstrates stable creep at lower temperatures, but as the temperature increases, its creep deformation accelerates rapidly. This is due to the relatively shorter molecular chains of Nylon 6 and weaker intermolecular forces, which allow for easier segmental motion of chains at elevated temperatures, leading to deformation.
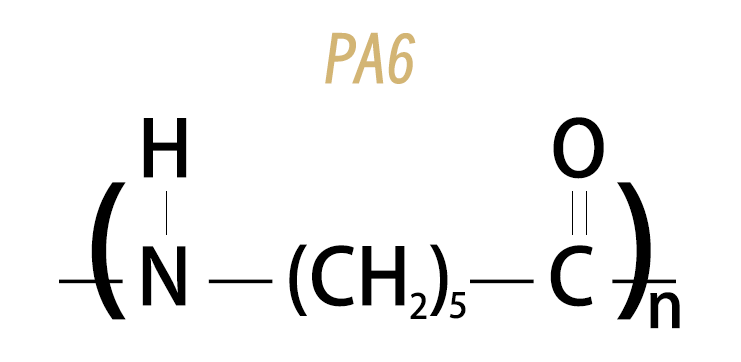
Nylon 66 (PA66): Compared to Nylon 6, Nylon 66 has longer molecular chains and a higher melting point, which means it generally shows less creep deformation at the same temperature. Its higher crystallinity and stronger intermolecular forces allow Nylon 66 to maintain better dimensional stability at high temperatures.
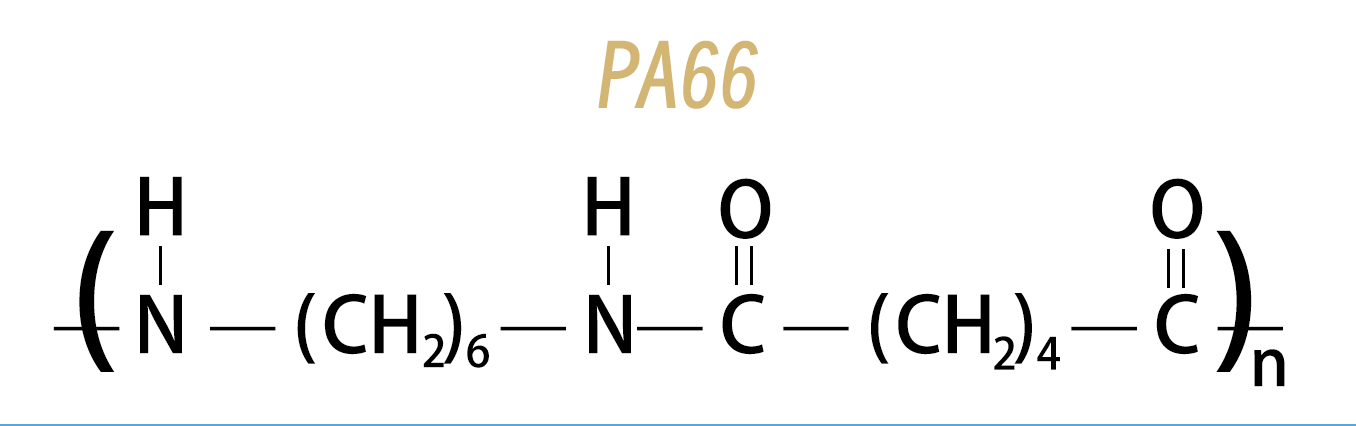
Understanding Creep for Optimal Cable Tie Selection and Use
Taking into account the creep of cable ties, it is clear that factors such as material selection, temperature, and stress all impact their durability in practical applications. The differing high-temperature creep behaviors of Nylon 6 and Nylon 66 underscore the importance of material choice for various circumstances. Particularly in high-temperature environments, Nylon 66 is more suitable due to its lower rate of creep and better thermal stability compared to Nylon 6. For applications subjected to high temperatures over long periods, heat-resistant cable ties, such as those that are heat-stabilized or high-temperature-resistant, are recommended. Understanding and accurately assessing these influencing factors are crucial for selecting the appropriate cable ties to ensure stable performance and durability.