Cable ties – these simple, small but versatile items are ubiquitous. They are unsung heroes that keep your tangled world of wires under control and keep cables and wires neatly organized. And when it comes to cable ties, nylon is a material that stands out, thanks to its strength, flexibility, and durability.
However, have you ever considered that cable ties come in various types of nylon? In this article, we’ll take a closer look at the main types of nylon used in cable ties. and delve into these types of nylon, giving you a clearer understanding of their properties, their strengths, and weaknesses. Additionally, we will provide tips on how to select the right nylon cable tie for your specific application.
What Material Are Cable Ties Made From
Cable ties are made from nylon, a type of polyamide polymer.
What is polyamide (nylon)
Polyamide or Nylon simply referred to as PA, is a high-performance polymer comprised of repeating units connected by amide linkages. It was invented in the early 1930s by Wallace Carothers and a team at DuPont. They successfully synthesized the first commercially viable nylon material.
It has many great qualities like being able to withstand high temperatures, insulate electricity, and resist wear, tear, heat, and chemicals. It comes as no surprise that polyamide (PA) finds widespread use in diverse fields.
The invention of polyamide (nylon) had a revolutionary impact on the modern chemical industry. Nylon and its derivatives have become significant materials widely used in textiles, plastics, engineering, and other fields.
Cable Ties Material
Different Types of Polyamide (nylon)
Polyamides can be created by a variety of monomers (which can be aliphatic, semi-aromatic, or aromatic).
Polyamide | Monomer(s) |
Polyamide 6 | Caprolactum |
Polyamide 66 | Hexamethylene Diamine/ Adipic Acid |
Polyamide 12 | Laurolactam |
Polyamide 46 | 1,4-Diaminobutane/ Adipic Acid |
Within the vast polymer family, several polyamides are commonly used in the production of cable ties, including PA6, PA66, PA12, and PA46. Among them, PA66 and PA6 are the most frequently utilized for manufacturing nylon cable ties, while PA46 offers the highest performance among these materials, it serve as excellent alternatives to metal and are well-suited for applications exposed to extreme conditions.
Cable Ties Material Properties
What is PA66?
Polyamide 66 (PA66), also known as nylon 66, was first synthesized in 1935 and entered production in 1938. It is one of the most commonly used thermoplastics for cable tie manufacturing. PA66 is formed by condensing hexamethylenediamine and adipic acid, which are two monomers, each containing six carbon atoms. The molecular structure of PA66 is as follows:
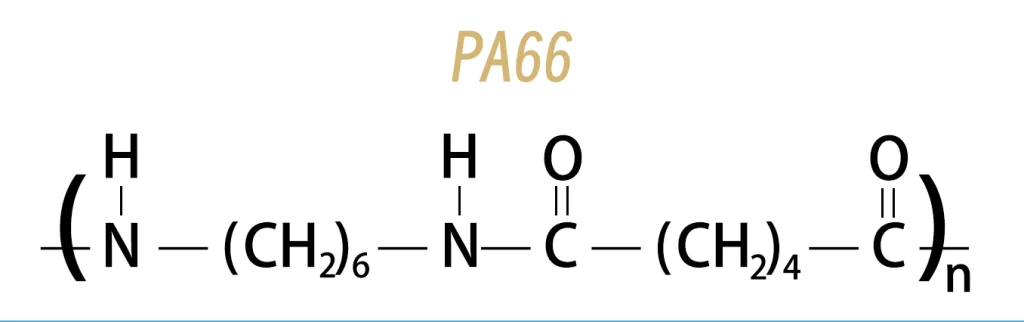
Characteristics
- Moderate Water Absorption
- High Mechanical Strength and Stiffness at Elevated Temperatures
- Good Abrasion and Wear Resistance
- Good Fluidity for Ease of Processing
- Excellent Impact Resistance, even under Low-Temperature
- Outstanding Fuel and Oil Resistance
- Good Fatigue Resistance
- Reliable Electrical Insulation Properties
It belongs to the category of linear polyamides, similar to polyamide 6 (PA6). However, PA66 has lower water absorption and higher heat resistance compared to PA6. The melting temperature of PA66 is around 260°C. It can maintain its shape consistently at temperatures up to 180°C and temporarily at temperatures up to 200℃.
Applications
PA66 cable ties find extensive applications in the textile industry, automotive manufacturing, mechanical engineering, electrical products, household appliances, and sports equipment. It is a favored engineering plastic for a variety of technical tasks due to its outstanding properties.
What is polyamide 46
Polyamide 6 (PA6), also known as nylon 6 or polycaprolactam, is one of the most widely used polyamides globally. It is synthesized through the ring-opening polymerization of caprolactam, and its molecular structure is as follows:
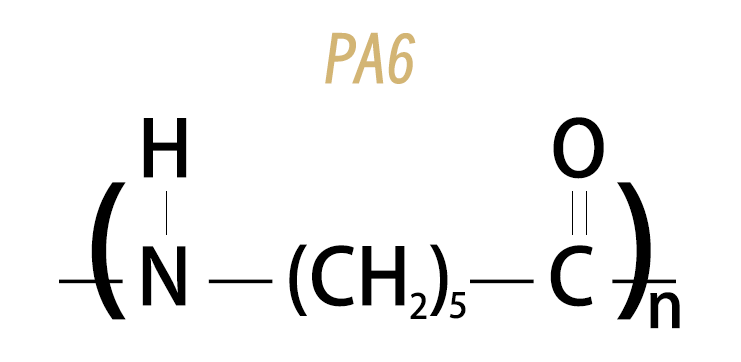
Characteristics
- High Water Absorption
- Chemical Resistance
- Cost-Effectiveness: PA6 is generally the most cost-effective compared to other polyamide
- Good Abrasion and Wear Resistance
- Optimal Fluidity for Ease of Processing
- Excellent Impact Resistance, even under Low-Temperature
- Outstanding Fuel and Oil Resistance
- Good Fatigue Resistance
- Reliable Electrical Insulation Properties
The Difference Between PA66 and PA6
Even though Nylon 6 and Nylon 66 are remarkably similar materials, they bear slight differences in their properties. These discrepancies largely stem from the disparity in their chemical structures.
Nylon 6 is made from a monomer that contains 6 carbon atoms, while Nylon 66 is synthesized from two monomers, each bearing 6 carbon atoms (hence the designation, Nylon 66). This nuanced divergence in their chemical led to their diverse characteristics.
Property | PA66 | PA6 |
Crystallinity | Higher, with larger crystalline regions | Lower, with fewer crystalline regions |
Melting Point | Higher, around 263°C | Lower, around 220掳C |
Water Absorption | Slightly lower | Slightly higher |
Mechanical Properties | Better rigidity, hardness, and wear resistance | Lower rigidity and toughness but higher hardness |
Low-Temperature Performance | More effective at low temperatures | Less effective at low temperatures |
Heat Resistance | Good heat resistance | lower heat resistance |
Processing Performance | Slightly lower flow | Good flow, easy to process |
Price | Relatively higher | lower |
Note: Specific properties can vary based on specific articles and cable tie manufacturers, so the above information is for general reference only. If you have specific application needs, it’s recommended that you directly contact us for more accurate information.
How to Choose from PA66 and PA6
When choosing between PA6 (Nylon 6) and PA66 (Nylon 66), it is important to understand the distinct properties of each and align them with the specific requirements of your application.
First, consider the operating environment: Will the component be exposed to high temperatures or harsh chemicals? PA66, with its superior heat stability and chemical resistance, maybe the better choice.
Second, evaluate the mechanical demands: Will the part need to withstand high mechanical stresses or repeated impact? While both materials are robust, PA66 generally offers higher tensile strength and stiffness.
Lastly, consider cost and availability. While both materials are widely used, PA6 is typically less expensive, which might make it more attractive for cost-sensitive applications.
Kindly note, while both PA6 and PA66 have their strengths and weaknesses, the final decision should be based on the specific application and constraints of your application. What’s more, we cable tie manufacturers can also further improve their performance by using appropriate additives to meet a wide range of application requirements.
What is polyamide 12
Polyamide 12, also known as PA12 or Nylon 12, is a semi-crystalline thermoplastic material with properties similar to Polyamide 11. It can be extracted from both fossil fuels and renewable resources. Compared to other polyamides, PA12 is a more expensive polymer.
Characteristics
- Lowest Water Absorption among Polyamides
- High Dimensional Stability
- High Electrical Properties.
- Superior Chemical Resistance
- Outstanding Cold Impact
- High Abrasion Resistance
- Broad Design Possibilities-With the availability of transparent PA12
Weakness
- Higher Cost Among polyamides due to their specialized attributes and manufacturing process.
- Lower Stiffness and Heat Resistance: This could potentially limit its use in certain applications requiring high rigidity and thermal endurance.
- Limited UV Resistance – It is therefore recommended to incorporate UV stabilizers or use UV-resistant grades of PA12 for such use cases.
Applications
PA12 cable ties are particularly used in applications requiring precision parts, where safety, durability, long-term reliability, and resistance to various conditions are important.
Such as the automotive industry, aerospace and defense, medical devices, outdoor applications, electronics, oil and gas industry, and marine applications.
What is PA46
PA46, also known as Polyamide 46 or Nylon 46, is a high-performance type of nylon with superb heat resistance, mechanical strength, and rigidity. PA46 cable ties with an excellent melting point (295°C), which is higher than that of PA6 and PA66. This high melting point makes PA46 an excellent choice for applications that require high strength and toughness at elevated temperatures.
Characteristics
- High Wear Resistance
- Excellent Mechanical and Thermal Performance
- Superior Wear Resistance
- High Resistance Against Radiation
- Good Electrical Insulation Properties
- Optimal Fluidity for Ease of Processing
Weakness
- Higher Cost
- Difficulty in Processing due to its high melting point of 295°C
- Color Limitations
- High Moisture Absorption
- Low-Dimensional Stability
- Discoloration at High Temperatures: Exposure to high temperatures can cause PA46 to darken or turn black.
Applications
PA46 cable ties are particularly suitable for applications requiring high-temperature resistance, excellent wear resistance, and superior mechanical properties.
Such as the automotive industry, electrical and electronics, industrial machinery, and aerospace.
Conclusion
Nylon cable ties, including those made from PA6, PA66, PA12, and PA46, each have unique properties that make them suitable for different applications. The choice between these materials depends largely on the specific requirements of your project, from the need for heat resistance to considerations for flexibility, strength, or water absorption.
Whether you’re in the automotive, aerospace, electronic, or industrial field, having a clear understanding of these differences can help you make an informed decision when selecting the most appropriate nylon cable tie for your needs.
At NIKE Plastics, we take these considerations to heart. As a leading cable tie manufacturer, we carefully control the performance parameters of our nylon cable ties based on the actual use scenarios of our end customers. This attention to detail ensures that our products deliver optimal performance, safety, and reliability, no matter the application. We are committed to delivering products that not only meet but exceed our customer’s expectations.