Are UV-resistant cable ties only available in black? This is a common misconception, especially in outdoor settings where UV-resistant cable ties are typically black. This is due to the traditional manufacturing process, which involves adding 2% carbon black to enhance the UV resistance of the ties, thereby improving their weather resistance.
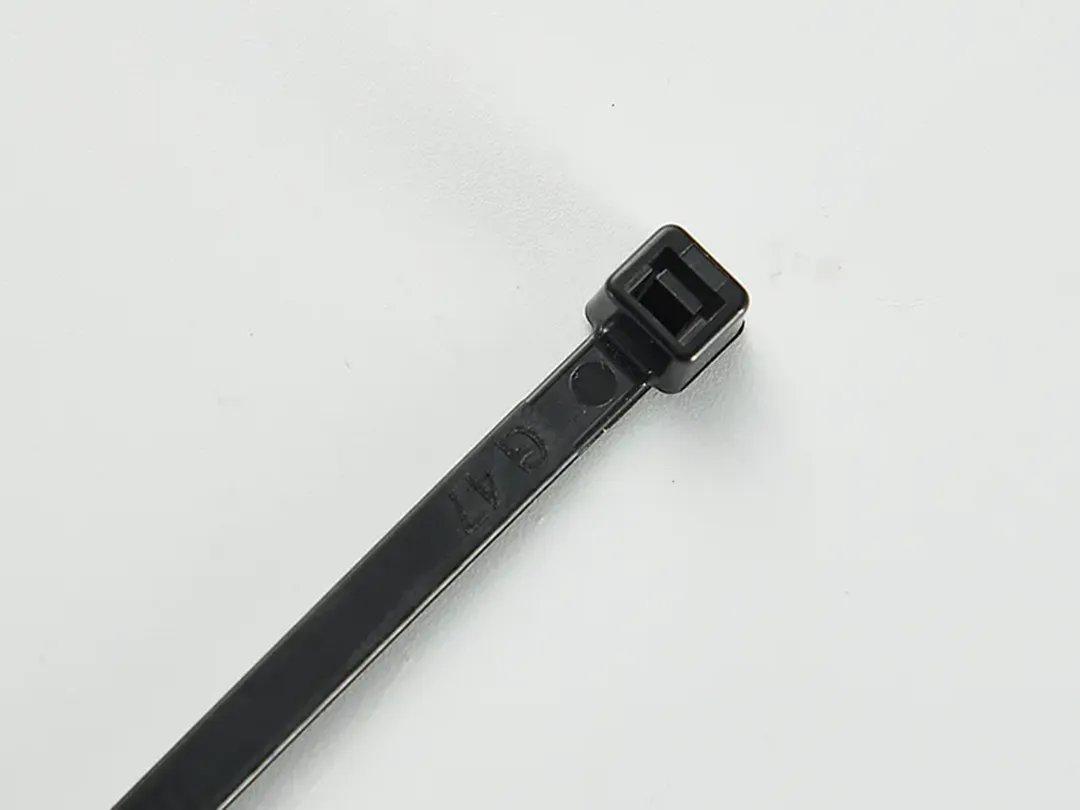
However, with advances in technology and the diversification of consumer needs, today’s UV-resistant cable ties are no longer limited to black. By adding special additives to the ties, they can improve UV resistance while maintaining their other mechanical properties and are available in more colors. The colorful UV-resistant cable ties not only meet functional needs but also greatly enhance their aesthetic appeal.
Below are some types of additives used in UV-resistant cable ties
What Additives Are Used in UV-Resistant Cable Ties?
Carbon Black – A Light Shield
The UV resistance of carbon black is due to its ability to absorb light. This effectively prevents the plastic from undergoing photo-oxidative degradation when exposed to sunlight. Carbon black converts light energy into heat, shielding nylon from certain wavelengths of radiation, and also acts as a free radical scavenger to prevent catalytic degradation.
The porous structure of carbon black particles further enhances their ability to absorb and scatter UV light, creating an effective UV barrier even with a small amount of carbon black. The stability of carbon black ensures that it retains its UV-absorbing and scattering properties under UV radiation, providing long-term and reliable UV protection, both indoors and outdoors.
However, carbon black has its drawbacks. Due to its color properties, UV-resistant cable ties produced with carbon black can only be black, which may not be aesthetically pleasing in some applications.
Apart from carbon black, other light-shielding additives include zinc oxide, titanium dioxide, and zinc-barium white.
Antioxidants
Antioxidants, when present in small amounts in polymer systems, can delay or inhibit oxidation, thereby increasing the lifespan of the polymer. Common plastic antioxidants can be categorized into five types based on their molecular structure and mechanism of action: hindered phenols, phosphites, thioesters, composite antioxidants, and hindered amine light stabilizers (HALS).
HALS antioxidants offer an effective solution. Rather than directly absorbing UV radiation, they function by scavenging free radicals that cause polymer degradation, thereby maintaining the mechanical properties of plastic products and extending their lifespan. Even in small amounts, HALS can have a significant effect.
UV Absorbers
UV absorbers are light stabilizers that absorb the UV portion of sunlight and fluorescent light sources. After absorbing UV radiation, these absorbers themselves do not change but rather convert high-energy UV light into harmless heat or longer-wavelength energy, protecting the polymer from damage. They effectively prevent plastics and other polymers from undergoing auto-oxidation reactions under light, thereby preventing degradation and deterioration, and maintaining the appearance and mechanical properties of the material.
Based on their chemical structure, UV absorbers are classified into salicylates, benzophenones, benzotriazoles, substituted acrylonitriles, triazines, and hindered amines. These absorbers provide long-term and stable UV protection for polymers through their respective mechanisms, ensuring their performance and lifespan.
Conclusion
The UV resistance of cable ties can be achieved by adding various additives, not just traditional carbon black. Different cable tie manufacturers may choose different options. As a result, UV-resistant cable ties are not limited to black and can come in various colors. This diversity not only broadens the market choices for cable ties but also meets the needs of different applications.