The tensile strength of zip ties is determined by several factors, which can be broadly divided into internal factors and external factors. Internal factors include the material, width, thickness, and manufacturing process of the zip ties. On the other hand, external conditions, like temperature and humidity, can also impact the strength. By understanding these internal and external factors, we can choose the most suitable cable ties for different conditions, ensuring the best bundling results and long-lasting durability.
The Factors That Determine the Tensile Strength of Zip Ties
Internal Factors
1. Cable Tie Material Type
Zip ties, also known as cable ties, are made from polyamide, commonly referred to as nylon. The two most common types of nylon used are Nylon 6 and Nylon 66. Nylon 6 is created through a single polymerization reaction of caprolactam, while Nylon 66 is made through a condensation reaction of adipic acid and hexamethylenediamine. This structural difference gives Nylon 66 longer carbon chains and more hydrogen bonds, which strengthen the molecular structure, providing greater mechanical and tensile strength.
Because of these hydrogen bonds, Nylon 66 performs better under tension. So, for the same size, Nylon 66 cable ties offer higher tensile strength compared to Nylon 6. For more information on the differences between these materials, refer to the article “Cable Ties: A Comprehensive Guide to Top 4 Materials.”
2. Width of Zip Ties
The width of a zip tie affects how much load it can handle. The wider the cable tie, the stronger the tensile strength it provides.
3. Thickness of Zip Ties
Increased thickness can enhance the overall strength of the tie, but if it’s too thick, it may reduce flexibility and make it harder to tighten and use. A balanced thickness provides a good combination of strength and flexibility for ease of use.
4. Production Process of Zip Ties
The quality and performance of zip ties also depend on the injection molding process, which can vary significantly between manufacturers. The key to injection molding is controlling the flow and cooling of the material within the mold, as this directly affects the consistency and strength of the final product. For more details on how this process works, refer to our previous article, “How Cable Ties Are Made.”
External Factors
1.Temperature
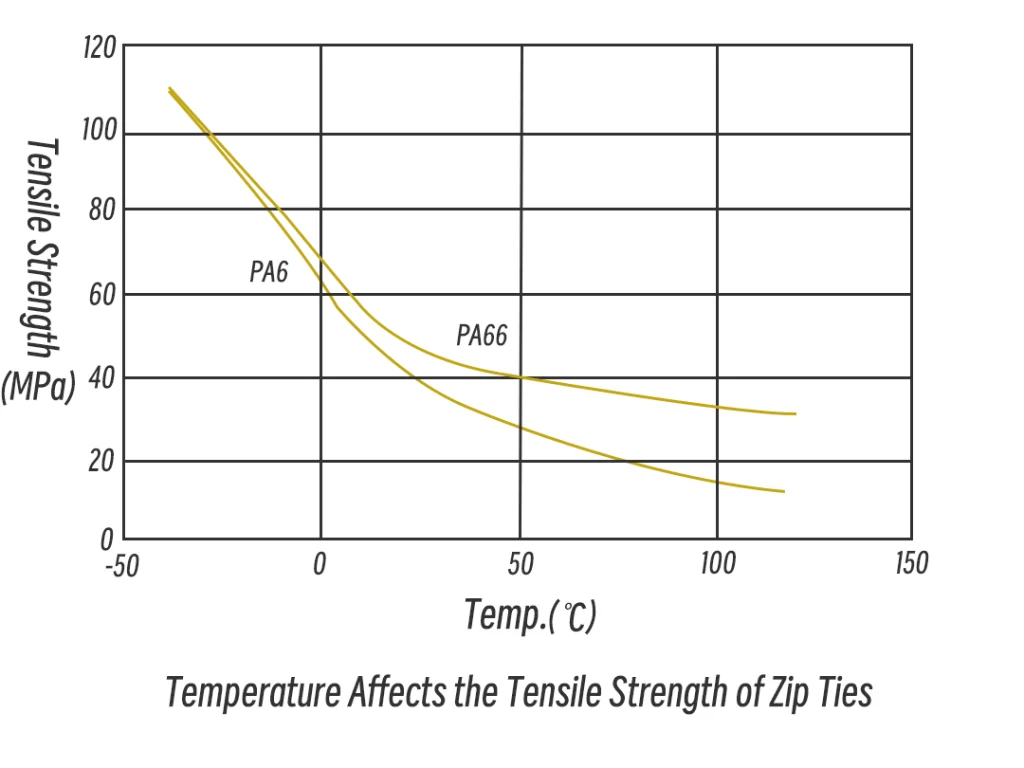
When the temperature rises, the molecules in nylon become more active and dynamic. This increased movement weakens the internal bonds of the material, allowing the molecular chains to move more freely. High temperatures also cause thermal expansion, which further reduces the tight bonding between molecules, leading to a decrease in overall strength.
In practical applications, especially in outdoor or high-temperature environments, it’s important to consider how temperature may affect the performance of cable ties. In such cases, using cable ties made from materials with higher heat resistance, like Nylon 66 instead of Nylon 6, or choosing specially treated materials, can improve their durability and reliability.
2. Humidity
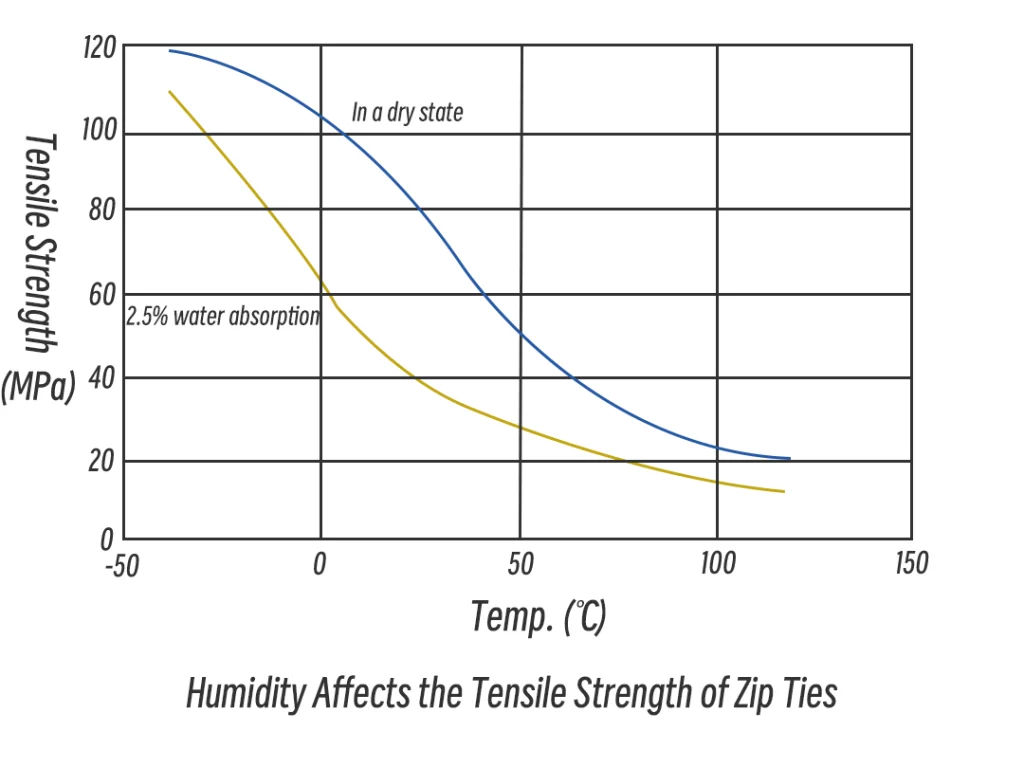
Nylon is a moisture-absorbing material, and its mechanical properties can be affected by the surrounding humidity. In high-humidity environments, nylon absorbs water and becomes softer, which can reduce its strength. As shown in the figure, Nylon 6 cable ties have stronger tensile strength when dry at various temperatures.
In practice, if cable ties need to be used in damp environments, it’s important to consider moisture protection measures or choose specially treated nylon materials to minimize the effects of moisture on performance.
3. UV Exposure
Prolonged exposure to UV rays causes nylon to degrade over time, leading to a gradual loss in mechanical strength, including tensile strength. UV light breaks down nylon’s molecular chains, resulting in material aging.
Using UV-resistant cable ties can help slow down this degradation and extend the life of the ties, especially in outdoor or high-sunlight environments.
Conclusion
In summary, the tensile strength of zip ties is influenced by both internal and external factors. Internal factors such as the width, thickness, material quality (whether virgin or recycled), and production process all play a role in determining the strength of the final product. Additionally, external factors like temperature, humidity, and UV exposure are critical in determining the tensile strength and overall performance during use. By considering both internal and external conditions, you can choose the most reliable zip ties for any situation.