Hot Runners vs Cold Runners in Cable Tie Production
In the injection molding process of nylon cable ties, the pivotal decision that cable tie manufacturers grapple with is whether to employ a cold runner or a hot runner system. This choice steers the production efficiency and directly correlates with the product quality and the eventual cost incurred. Therefore, making a wise choice is paramount. Today, we at NIKE PLASTIC, representing the cable tie manufacturers, will acquaint you with the cold runner and hot runner in the nylon cable tie injection molding process.
What is Cold Runner System
A cold runner refers to the unheated melt channel from the equipment nozzle to the mold cavity. Throughout the injection process, this segment of the melt channel gradually cools and ultimately solidifies due to its lower temperature, hence it is dubbed a “cold” runner, signifying its lower temperature compared to a hot runner in maintaining the molten state of the melt.
Why Choose Cold Runner System
- Simpler Structure: Given the absence of heating elements, its design and maintenance are relatively straightforward.
- Lower Cost: The simpler structure translates to lower initial equipment costs and maintenance fees.
- High Flexibility: Adaptable to a wide array of plastic materials, including some special polymers.
- Quick Color Change: Swapping plastic colors is generally quicker and easier since there is no molten plastic lingering in the hot runner.
Limitations of Cold Runner System
- Waste Generation: Post each injection cycle, the plastic in the runner usually needs to be removed and treated as waste, augmenting material costs.
- Longer Cycle Time: The necessary cooling of the plastic in the runner potentially elongates the overall production cycle.
- Temperature Control: Premature cooling of the plastic before it reaches the mold cavity necessitates meticulous temperature control to assure product quality.
What is Hot Runner System
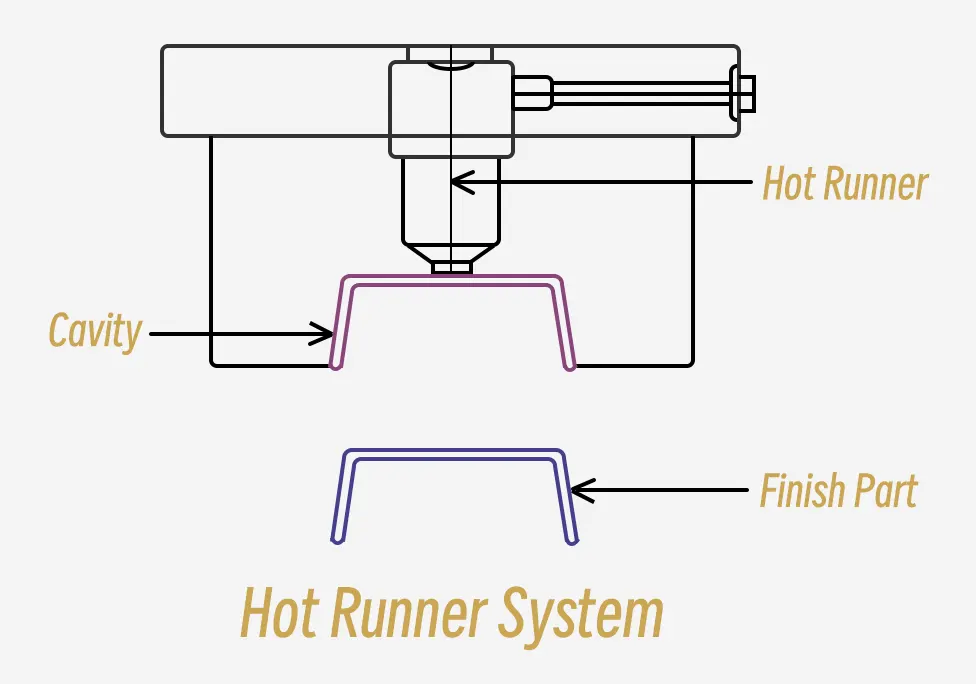
A hot runner system is essentially analogous to a hot water piping system but caters to melt nylon instead of water. During injection molding, the hot runner employs heating elements to continually maintain the plastic’s molten state from the injection machine to the mold cavity. In layman’s terms, it serves as a “hot pathway,” aiding the plastic in reaching the correct location while sustaining its molten state and fluidity.
Why Choose Hot Runner System
- Waste Reduction: The continual molten state of the plastic throughout the procedure virtually eliminates waste generation.
- Shorter Cycle Time: The heating system facilitates swift conveyance of the plastic into the mold, reducing the entire molding cycle.
- Uniform Material Flow: The hot runner system’s ability to heat the plastic uniformly yields more consistent quality products.
- Suited for Complex Products: Hot runners offer better control and higher quality products for intricate or multi-cavity molds.
Limitations of Hot Runner System
- High Cost: With a higher cost of the mold and the subsequent maintenance costs
- Complex Maintenance: The involvement of electronics and heating elements might call for meticulous maintenance.
- Not Suitable for All Materials: Certain heat-sensitive or easily degradable materials might not be applicable.
- Challenging Color Change: Residual molten plastic in the system can make the color change process more complex and time-consuming.
Choosing the Right Runner System for Nylon Cable Ties Production
In conclusion, when choosing the runner system for cable tie production, it is imperative to consider multifaceted factors including the product demand volume, material type, and costs. For instance, the hot runner system, renowned for its stable quality production and material-saving attributes, is generally more conducive to those high-quality requirements or mass production. Meanwhile, the cold runner system, celebrated for its flexibility and relatively lower operational costs, might be more suitable for small-scale, diversified production. Each runner mold holds its unique advantages and limitations. Therefore, it is crucial to weigh these aspects carefully, aligning the choice with the specific production needs and long-term goals of the manufacturing process.